Precision plastic molds, also known as combination molds used for compression, extrusion, injection, blow molding, and low foam molding, are essential for shaping plastic parts of different shapes and sizes through coordinated changes in the mold's cavity, core, and auxiliary molding systems. To meet the requirements of molded parts, attention must be paid to certain aspects when selecting precision plastic molds, along with corresponding demands. Below are the six major requirements for choosing the most suitable precision plastic molds:
1. High Corrosion Resistance: Many resins and additives have a corrosive effect on the surface of mold cavities, causing metal dissolution, peeling, deterioration of surface conditions, and degradation of part quality. Therefore, it is preferable to use corrosion-resistant steel or apply chrome plating and nickel plating to the mold cavity surface.
2. Excellent Wear Resistance: The gloss and precision of plastic parts' surfaces are directly related to the wear resistance of the mold cavity surface. Especially when certain plastics contain fiberglass, inorganic fillers, and certain pigments, they flow rapidly through runners and mold cavities together with the plastic melt, resulting in significant friction on the mold cavity surface. If the material is not wear-resistant, it will quickly wear out, compromising the quality of the parts.
3. Good Dimensional Stability: During plastic molding, the temperature of the mold cavity needs to exceed 300°C. Therefore, it is best to use tool steels that have been appropriately tempered (heat-treated steels). Otherwise, changes in the material's microstructure may occur, leading to dimensional changes in the plastic mold.
4. Ease of Machining: Mold parts are mostly made of metal materials, with some structures being quite complex. To shorten the production cycle and improve efficiency, it is necessary for mold materials to be easily machinable into the shapes and accuracies required by the drawings.
5. Excellent Polishing Performance: Plastic parts often require good gloss and surface condition. Therefore, the roughness of the mold cavity surface must be extremely low, necessitating surface treatments such as polishing and grinding. Hence, the selected steel should be free of rough impurities and pores.
6. Minimal Influence from Heat Treatment: To enhance hardness and wear resistance, plastic molds generally undergo heat treatment. However, this treatment should minimize dimensional changes. Therefore, it is advisable to use pre-hardened steels that are machinable.
These considerations are crucial for selecting precision plastic molds that can effectively meet the demands of molding components.
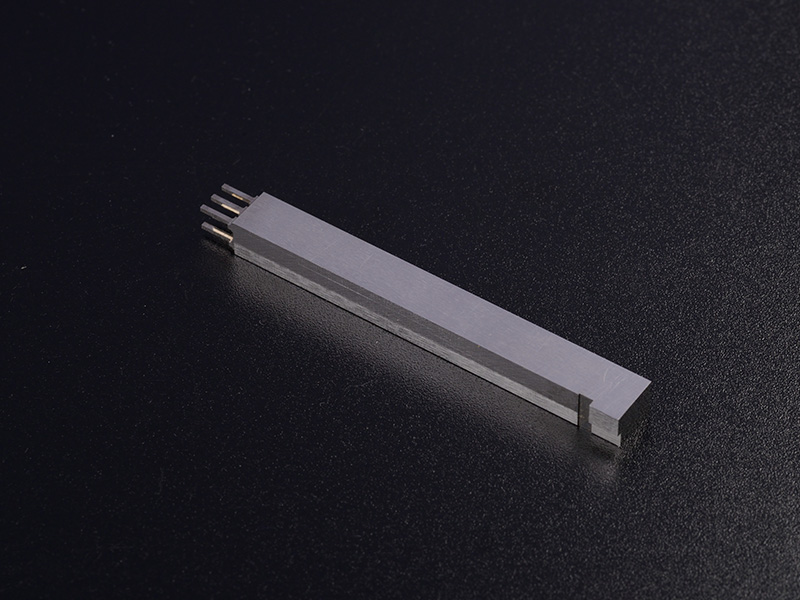