In today's technological landscape, precision plays a crucial role in various industries, particularly in manufacturing and engineering. Precision Electrical Discharge Machining (EDM) is a cutting-edge process that enables the production of intricate and highly accurate components. This essay aims to explore the concept of Precision EDM Processing, its applications, working principle, and the benefits it offers.
Understanding Precision EDM Processing:
Precision EDM Processing refers to the utilization of electrical discharges or sparks to shape and refine materials with incredible precision. It involves the controlled erosion of conductive materials using a series of rapid electrical discharges. The process involves a complex interplay between a specialized tool electrode and the workpiece, with a dielectric fluid acting as a medium for spark generation and dielectric flushing.
Applications of Precision EDM Processing:
Precision EDM Processing finds numerous applications across a wide range of industries, including aerospace, automotive, medical, and tooling. It is particularly useful when dealing with hard and brittle materials such as hardened tool steels, tungsten carbide, and titanium alloys. Some common applications of Precision EDM Processing include:
Mold and Die Manufacturing: Precision EDM Processing is extensively used in mold and die manufacturing industries to create complex cavities, intricate shapes, and fine details.
Aerospace Components: The aerospace industry utilizes precision EDM to produce critical components like turbine blades, fuel nozzles, and engine parts with exceptional accuracy.
Medical Devices and Implants: Precision EDM enables the production of intricate medical devices, such as surgical instruments and dental implants, ensuring the highest levels of accuracy and quality.
Working Principle of Precision EDM Processing:
Precision EDM Processing operates on the principle of electrical discharge between the tool electrode and the workpiece. The two electrodes are brought together within a dielectric fluid-filled gap, typically deionized water. The process commences when an electric potential is applied across the electrodes. This potential difference generates a series of electrical discharges or sparks between the electrodes, causing localized melting and vaporization of the workpiece material. These discharges occur at extremely high temperatures, around 8,000 to 12,000 degrees Celsius, resulting in the controlled erosion and removal of material from the workpiece, following the shape of the tool electrode.
Benefits of Precision EDM Processing:
Precision EDM Processing offers several advantages that make it an invaluable manufacturing process:
Unmatched Precision: Precision EDM can achieve tolerances in the range of microns, enabling the production of highly intricate and accurate components.
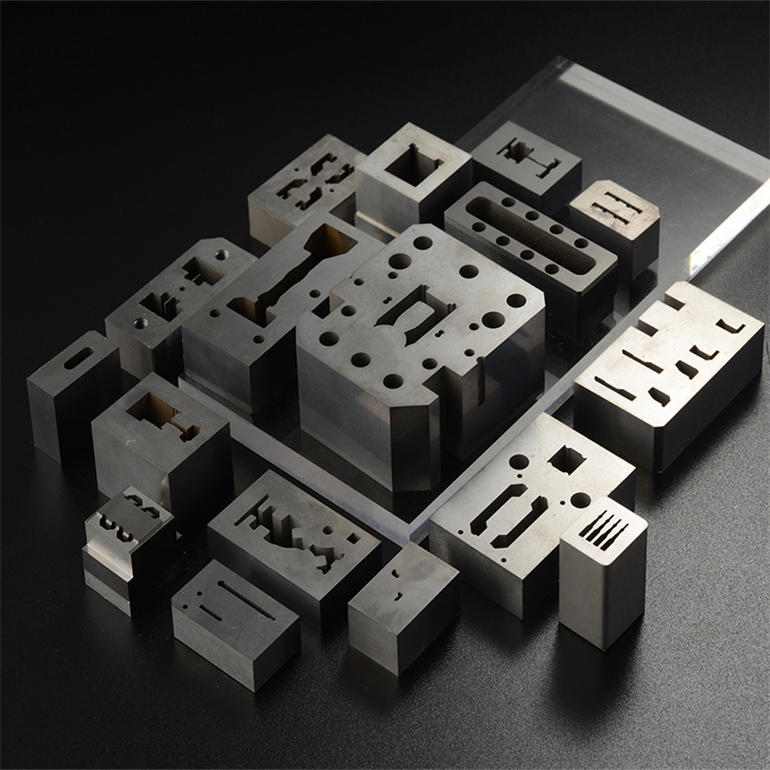
Versatility: It can efficiently process a wide variety of materials, including heat-treated and exotic alloys that are typically challenging using conventional machining methods.
Surface Finish: With precision EDM, it is possible to achieve exceptional surface finishes, eliminating the need for secondary finishing operations.
Cost-Effective: Despite its precision, Precision EDM Processing can be a cost-effective manufacturing method. It reduces material waste, as it is a non-contact process, and avoids the need for expensive tooling.
Precision EDM Processing is a revolutionary technology that has transformed the manufacturing landscape by enabling the production of highly accurate and intricate components. Its applications across various industries have opened doors to new possibilities and advancements. With its impressive precision, versatility, and cost-effectiveness, Precision EDM Processing continues to be an invaluable tool for achieving excellence in modern manufacturing processes.